The Product Development Lifecycle
A product goes through several stages in its lifecycle before it becomes retail-ready. OEMs and their contract manufacturers (CMs) need to follow eight stages to design and manufacture a product that’s competitive, no matter their industry or niche. This eight-step process ensures that your product not only does what you need it to do, but that it’s also safe, compliant, and cost-effective.
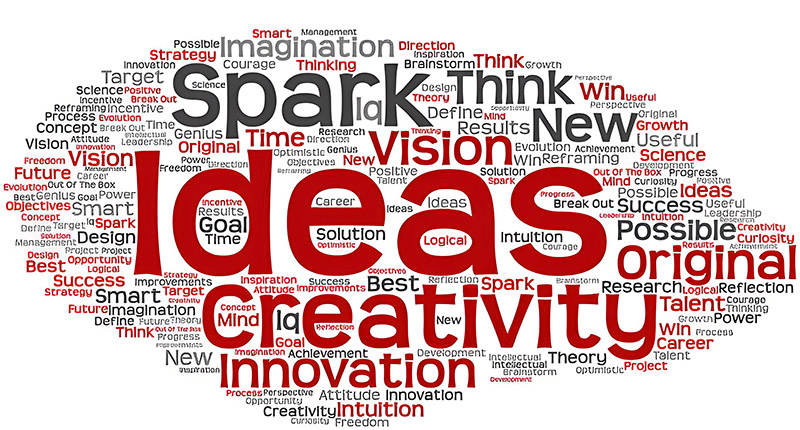
Step 1: Conceptualization
Ideation is important because the idea affects every single aspect of the product. You need a great idea to create a mockup, a prototype, and throughout the entire manufacturing process.
Step 2: Form, Fit, and Function
In the second stage of the product development lifecycle, your team needs to create product specifications. This is also known as the form, fit, and function stage, where your designers go over the PRD to iterate digital versions of the product.
In this stage, your design team will mock up the product with digital renderings.
Step 3: Prototyping
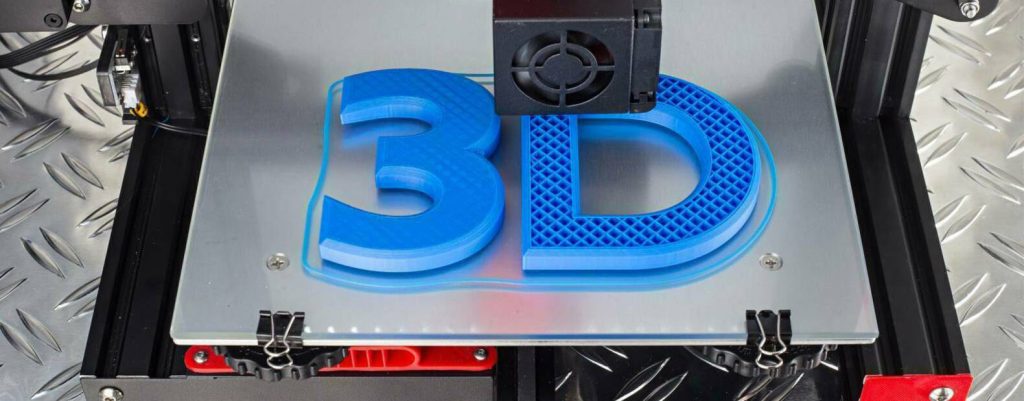
A great way for OEMs to reduce the cost of prototyping is with 3D printing. It focuses solely on function, churning out multiple iterations of a product for a very low cost.
Step 4: Beta Prototype and Proof of Concept
In this stage, you’re looking at how all the components of your product come together in the physical world. This means creating betas in varying forms, sizes, and colors if necessary.
Step 5: Validation and Quality Assurance
By the end of the fifth phase of the product life cycle, you’ll have a good idea if this product is ready to hit shelves. But you need to make sure that it hits several criteria before you look for a manufacturer.
Step 6: Find a Quality Manufacturer
You likely have a network of manufacturers that you know and trust. It’s essential to find a manufacturer who’ll follow through on your design, follow safety protocols, and protect your intellectual property.
Step 7: Manufacture the Product
It’s tempting to let your manufacturer handle things from here, but it can easily go off the rails without hands-on management. You should understand how the factory works and that it’s capable of churning out consistent products. In fact, it’s not unusual for many OEMs to visit factories for weeks at a time to ensure everything runs smoothly.
Whatever you do, stay involved with the manufacturing process. Make sure the raw materials, product quality, and production processes are followed to a tee. If the manufacturer is having problems, you’ll discover them sooner and potentially save millions in production costs.
Step 8: Optimize Product Development
It’s critical to take feedback from your customers, too. For example, if a certain component doesn’t last long enough, that’s important feedback for your product team.
In the optimization phase, it’s also important to optimize the manufacturing process. Work with your manufacturer to see if anything can be automated to drive down prices or time to market.
Interested in OEM? Contact us now
Allow OEM by Singtai to be your trusted partner in making the correct “make or buy” decisions.